Table of Contents Hide
-
1
The Impacts of Device Self-heating
- 1.1 Thermal droop
- 1.2 Lumen depreciation
- 1.3 Color shift
- 1.4 Packaging material degradation
- 1.5 LED failure
- 1.6 Circuit failure
-
2
Heat Generation in LED Lighting Systems
- 2.1 Die-level heat
- 2.2 Phosphor-level heat
- 2.3 Circuit-level heat
- 3 Thermal Design
- 4 Heat Transfer Mechanisms
-
5
Package Level Thermal Management
- 5.1 Junction-to-substrate
- 5.2 Solder joints
- 6 System Level Thermal Management
- 7 Active Cooling
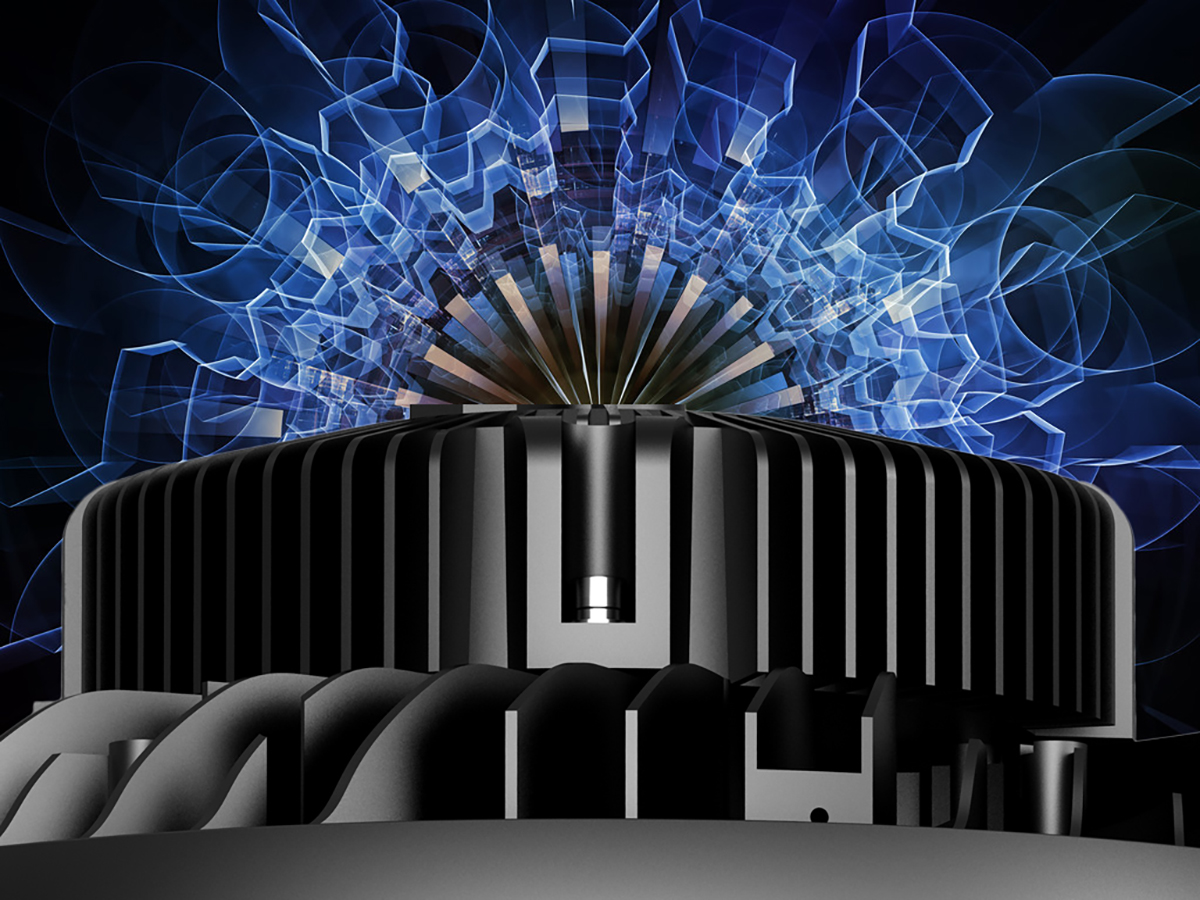
High temperature is the most important failure accelerator in LED lighting systems. Thermal management was historically not a design factor for incandescent, florescent or metal halide lamps. The waste energy produced in these lamps is dissipated as infrared energy in the radiant beam of light and as heat that requires no additional management. LEDs do not radiate thermal IR energy in its light spectrum, but the waste energy generated from electro-optical and wavelength conversion is all converted into non-radiative thermal energy that remains trapped in the semiconductor diodes. Hence dissipation of the device-level thermal energy becomes an integral part of an LED system design.
The Impacts of Device Self-heating
When an LED produces optical radiation, it is also heating up itself. Despite the unrivalled light output of LEDs as compared to their predecessors, LED technology still faces efficiency challenges. The highest efficiency LEDs that are commercially available convert only about 50% -60% of the electrical power into light, the rest is released as heat that must be routed away from the semiconductor devices. Excess heat buildup within the device will accelerate the degradation process, affect optical performance and lead to system failures.Thermal droop
Operating an LED above the maximum allowable junction temperature will increase carrier delocalization and non-radiative Auger recombination in the LED, which results in a temperature dependent reduction in external quantum efficiency (EQE), known as thermal droop. Thermal droop in InGaN LEDs can lose up to 25% of optical power, and in AlGaInP LEDs the light output can drop 70%.Lumen depreciation
While thermal droop is short-term (reversible) effect, continuous operation at elevated temperature can significantly accelerates lumen depreciation, which is an irreversible gradual reduction in light output over time. For every 10 °C increase in junction temperature, the useful life (defined as 70% lumen maintenance) of an LED will be reduced by 30% to 50%.Color shift
The operating temperature of an LED is inversely proportional to the semiconductor bandgap which is the difference in energy between the conduction band of the negative region and valence band of the positive region. In addition to external interaction with phosphors and encapsulants, the frequency of light (wavelength) produced by the LED is governed by this bandgap energy. In general, for every 10°C rise in the junction temperature of an LED, the dominant wavelength of the light will increase one nanometer. Accordingly, when an LED experiences a big increase in its operating temperature, a noticeable color shift toward the higher end of the spectrum will occur.Packaging material degradation
Operating outside rated conditions can lead to thermal degradation of materials utilized in the LED packages, such as phosphors, encapsulatants, and plastic lenses. The consequence is a permanent chromaticity shift or spectral change due to carbonization or discoloration of the polymer material.LED failure
A dramatic change in the coefficient of thermal expansion (CTE) will causes the epoxy encapsulant of an LED package to expand and contract. A catastrophic failure will occur due to the premature wear-out and breakage of the bonding wire within the LED package.Circuit failure
Thermally induced stresses can cause a high CTE at the interconnection level and thus is likely to compromise solder joint reliability. A damaged or faulty solder joint can cause an electrical open circuit that ends up in a complete failure of the LED.Driver failure. In co-located systems, the thermal load from the LED module can dry out the liquid electrolyte in an electrolytic capacitor. Electrolytic capacitors are often used in driver circuits as an energy storage element to absorb voltage surges and reduce ripple. Exposure of the capacitor to heat will accelerate the reduction in capacitance and thus cause the driver to malfunction.
Heat Generation in LED Lighting Systems
Wherever there's energy conversion there is an energy loss. LEDs are low-voltage, current-driven devices that operate in a forward bias. AC power provided by an electric utility must first be rectified to become DC power, which is then regulated into a constant current before using it to drive LEDs. When a forward voltage is applied to the diode, electrical current is passed through the p-n junction, electrons flowing from negative to positive recombine with holes and release light. This effect is called electroluminescence. A subsequent photoluminescence may take place to down-convert a portion of the short wavelength. The down-converted wavelength mixes with the unconverted short wavelength to produce the desired white light. A complete light emission process for an LED lighting system, therefore, consists of AC-DC power conversion, electro-optical energy conversion, and wavelength conversion. Energy loss occurs in every stage, and, as mentioned previously, virtually all the energy that is wasted in these stages is converted into heat.Die-level heat
The die-level heat is generated primarily as a result of the injection efficiency losses, internal quantum efficiency (IQE) losses and photon extraction losses occurring at the semiconductor die. Injection efficiency is the proportion of electrons which pass through the junction and form electron-hole pairs at the active semiconductor region. Recombination of injected electrons and holes also takes place non-radiatively, IQE is the ratio of radiative photons to the electron-hole pairs injected into the active semiconductor region. Incomplete extraction of photons from the semiconductor material leads to heat generation at the die. In light-emitting diodes, non-radiative Auger recombination increases when injection current density increases. Efficiency droop that is resulted from high drive current operation also translates to increased die-level heat.Phosphor-level heat
In general lighting applications, white light is almost exclusively produced by phosphor-converted LEDs. These LEDs consist of an InGaN LED chip coated with an organic polymer containing a yellow YAG:Ce phosphor. The phosphor is pumped by a blue wavelength source and converts some portion of the short wavelength light (blue) into light of longer wavelengths (yellow), thereby broadening the emission spectrum and making the mixture of blue and yellow light appear as white light. This wavelength conversion process produces a significant amount of heat due to Stokes losses. Depending on the correlated color temperature (CCT) of the LED, about 15% to 40% of radiant power absorbed by the phosphor layer is converted to heat. Phosphors are typically formulated with polymers which act as a binder to keep the phosphor in place. Unfortunately, the polymer resin exhibits a very low thermal conductivity. Hence, the phosphor layer has the highest temperature within phosphor-converted LED packages and thermal quenching is an inevitable effect for the phosphor layer.Circuit-level heat
The efficiency of the LED driver plays an important role in determining the thermal stresses of the co-located systems where the driver is mounted relatively close to the LEDs. Switched mode power supplies typically has a conversion efficiency around 90% and generate a moderate amount of heat. The problem comes from the increasingly widespread use of low cost, low efficiency and low output quality linear power supplies. All linear power supplies require a supply voltage at least some minimum amount higher than the desired output voltage. The minimum voltage required across the linear regulator to maintain regulation is called a dropout voltage. In this mode of operation, the dropout voltage is simply thrown away a heat. Linear power supplies have a high dropout voltage which typically accounts for 15% - 30% of the supply voltage. This means up to 30% of the power is wasted and dissipated as heat. As there's a trend toward driver-on-board (DOB) luminaire design that uses linear power supplies, the LEDs that are mounted on the same printed circuit board (PCB) with the driver circuit are loaded with a thermal stress higher than ever.Thermal Design
Thermal management for LED lighting systems is aimed at maintaining the junction temperature of the LEDs and the operating temperature of other system components below a set limit. Aside from causing performance degradation, premature failures and irreversible damages, the temperature at the junction between the positive and negative layers of the semiconductor diode is the single most important factor in establishing LED spectral and electrical performance. Efficient removal of heat from the semiconductor junction to the ambient environment helps achieve desired optical performance, maximize energy efficiency, and increase the service life of the LEDs and other system components. The junction temperature of an LED is primarily affected by three parameters: drive current, thermal path, and ambient temperature. Since ambient conditions are a design requirement rather than a tunable element, the thermal design effort naturally goes into creating an efficient thermal path and optimizing the electrical specifications.Drive current selection has an inherent contradiction. As long as the mechanism of high current efficiency droop is not triggered, LEDs can be driven harder to increase luminous efficacy. When the LED array is powered by a drive current higher than nominal conditions, there is increased lumen output but that typically comes with a very high heat flux density. Consequently, the drive current should fall within thermal constraint of the lighting system or additional thermal capacity must be provided to compensate for the increased heat generation.
The ability of an LED system to dissipate heat is ultimately dependent upon the design of the thermal path from the die to the surroundings. The thermal path must be dimensioned to accommodate the applied power load. Thermal resistance of all the elements that make up the thermal path should be kept as low as possible to ensure the waste heat is efficiently transferred to the ambient air without excess thermal buildup within the LED.
Thermal energy can only be discharged from a warmer material to a cooler material. In addition to the design of the thermal path, the amount of heat that can be removed from the LED junction also depends upon the ambient temperature. It can be very challenging to operate LED luminaires in iron and steel foundries, boiler rooms, brick-firing and ceramic plants, glass manufacturing facilities, rubber products factories, commercial kitchens, and other environments with high air temperatures or radiant heat sources. In such cases the thermal design must take the thermal stability of critical system components into consideration. The substrate of an LED package needs to be thermally conductive enough to dissipate the heat away from the LED die. Thermal stability of the phosphor encapsulation is also very important. Not only does it require an excellent resistance to thermal quenching, its thermal diffusivity should also be high in order to efficiently dissipate the Stokes heat generated in the phosphor. The real-life thermal performance of the LED driver is equally essential in LED luminaire thermal management. Electrolytic capacitors, which're high temperature sensitive, should be replaced by air-core magnetics, ceramic capacitors or other thermally stable components so as to survive high ambient temperature conditions.
Heat Transfer Mechanisms
There are three mechanisms for transferring heat between elements at different temperatures: conduction, convection, and radiation.Thermal conduction is energy transfer from the higher temperature to the lower temperature region across a solid material by direct contact. The thermal conduction potential of materials, which is expressed as thermal conductivity, is dependent upon the thermal characteristic of the material and its geometry. Hence, thermal conduction capacity of a thermal path can be improved by maximizing material thermal conductivity and effective surface area of the thermal path. Metals are the best thermal conductors with conductivity in the range between 100 and 400 W/mK. Air gaps should be avoided along the thermal transfer path because air is a very poor conductor of heat (about 0.025W/mK). Conduction is the most significant mechanism of heat transfer within an LED lighting system in which solid components are designed in mechanical contact.
Thermal convection is the transfer of heat through the physical movement of molecules from a solid matter boundary to a fluid, which can be a liquid but is more typically air. The amount of convective heat transfer is dependent upon an effective surface area and the mobility of the air or liquid. Thermal convection that takes place as a result of gravitational fluid flow is referred to as natural convection. Thermal convection which is facilitated by external means such as fans or blowers is known as forced convection. The heat transfer coefficient is used to quantitatively characterizing heat flow across a fluid/solid interface. Natural convection usually has a heat transfer coefficient in the range of 5-20 W/m2 K. With forced convection, the heat transfer coefficients can be as high as 100 W/m2 K for air and up to 20,000 W/m2 K for liquids. In LED systems, convection is the main mode of heat transfer to transfer heat from the heat sink to the ambient air.
Thermal radiation refers to heat transfer through electromagnetic waves, as opposed to using a carrier medium in conductive and convective methods. Radiative heat transfer has a very strong dependency on the emissivity and temperature of the surface material. The emissivity of a material, which relates to the ability of its surface to emit energy by radiation, is determined by the physical properties and the geometrical characteristics of the surface material. Non-metallic and non-transparent materials generally exhibit a higher emissivity than metal surfaces. A painted or anodized surface will have a greater emissivity than a shiny, unpainted one. The higher the surface temperature and larger the surface area of a luminaire housing, the more heat will be emitted in the form of IR radiation. However, radiative heat transfer won't become noticeable until the surface temperature rises above a temperature of 100 °C. In LED lighting systems, radiation contributes very little to system heat transfer since the surface temperatures are relatively low and most LED luminaires have a small surface area.
Package Level Thermal Management
Package level thermal management handles the junction-to-substrate thermal resistance and thermal performance of solder interconnect. Heat which is generated at the semiconductor junction must be drawn away through the bottom of the LED die, the lead frame or ceramic substrate, to the solder joint. The most efficient heat transfer mechanism on this level is thermal conduction.Junction-to-substrate
The junction-to-substrate thermal resistance comes from the joint between the LED die and submount substrate. Mid-power LED packages in which the die is mounted on a silver-coated metal lead frame have a less robust construction than high-power LEDs based on ceramic substrates. The dominant process for interconnecting the positive and negative electrodes of the semiconductor chips to the lead frame or the electrodes of the carrier substrate is an ultrasonic welding process called wire bonding. Gold is the most widely used metal used in semiconductor packaging because of its resistance to surface corrosion, high bonding strength, and good electrical and thermal conductivity. Wire bonding, however, limits power density of LEDs. Chip scale packages (CSPs) eliminate wire bonding and remove the need for die attach on a submount substrate, allowing them to achieve a considerably lower thermal resistance than conventional LEDs.Solder joints
A considerable amount of heat produced around the LED junction needs to be transferred to the lighting system. Thus the reliability and thermal performance of the solder joint between the LED package and PCB become very critical. Solder joint reliability not only depends on the solder paste composition and solder joint geometry, but also involves many metallurgical and process parameters such as melting point, surface tension, time for flux activation and volatilization, ramp rate, pre-heat and peak temperatures, soak and hold times, and cooling rate. The temperature profile of a reflow process plays a decisive role in the wetting behavior, interface chemistry, and metallurgical microstructure of the solder joint. In high power density applications, thermally induced stresses from CTE mismatches can lead to thermomechanical failures. The difference in thermal expansion coefficients between the LED package and the PCB material therefore should be given serious consideration to.System Level Thermal Management
System level thermal management handles heat transfer from the PCB through the heat sink to the ambient. Thermal design on this level revolves around providing an adequate path to convection by enhancing thermal conductivity of all components along the thermal path and increasing the heat transfer coefficient of the heat sink. Thermal management components that form this heat flow path include the PCB, thermal interface material (TIM) and heat sink.Printed circuit boards
Typically, LEDs are surface mounted on a printed circuit board to which the heat dissipated out of the bottom of the LED packages is conducted via solder interconnection. Conventional PCBs are made from FR4 (fiber glass reinforced epoxy laminate) sheets which have excellent electrical insulation properties but have a very poor thermal conductivity (0.4-1 W/mK). Many FR4 circuit boards are designed with thermal vias which can be open, plugged, filled, or filled and capped plated through holes (PTHs) to reduce thermal resistance. However, FR4 PCBs cannot diffuse excessive heat when high brightness LEDs are densely packed into a small form factor and the junction temperature is generally around 100°C. Heat that flows to the FR4 PCB does not spread in the in-plane direction. Thermal buildup occurs over the FR4 PCB to form local hot spots. As such, FR4 PCB's poor efficiency in thermal conduction introduced the prevailing use of metal core printed circuit boards (MCPCBs) in LED systems.An MCPCB is manufactured from a metal sheet (usually aluminum, sometimes copper) coated with a dielectric layer, which is then covered with copper layer. The aluminum base sheet functions as a heat spreader. The top copper layer acts as a circuit layer patterned to match the interconnect requirements of the LEDs. Because copper and aluminum are both efficient in thermal conduction, what distinguishes the MCPCBs from different brands is the construction of the dielectric layer. Sandwiched between copper and aluminum layers, the dielectric layer offers electrical isolation, bonds the metal layers and provides heat transfer. A high performance MCPCB requires its dielectric layer to have high thermal conductivity, electrical breakdown strength, and adhesion strength with copper and base metal plate. In the majority of instances the dielectric is a resin matrix which often contains a second phase dielectric material such as ceramic particles for the purpose of increasing thermal conductivity. The thermal conductivity of the dielectric layer can be 16 times higher than conventional FR4 dielectric.
Thermal interface materials (TIM)
Thermal interface materials (TIMs) are used to fill interfacial air gaps and voids between the heat sink and the PCB. Air gaps and voids are very poor conductors that could undermine the efficiency of a thermal path. TIMs replace the trapped air with a much higher thermal conductivity material, thereby reducing thermal contact resistance (TCR). A variety of thermal interface materials can be used to thermally coupling thermally coupling the interfaces. The TIM can be thermal greases, thermal adhesives and epoxies, phase change materials, thermally conductive pads/films, thermal adhesive tapes, metallic films and foils, or carbon-based TIMs. Thermal greases, with a thermal conductivity range of 1-5 W/mK, are made from a silicone-based matrix loaded with conductive fillers, such as aluminum oxide, zinc oxide, or boron nitride. This type of TIM has a good surface wetting characteristics (low contact resistance at the interfaces) and flows easily to fill up voids at the interfaces. PCMs combine the wetting properties of a grease with the convenience of handling and peel-and-stick application of pads. However, they have a lower thermal conductivity than greases (0.1-3 W/mK). Carbon-based TIMs, such as those fabricated using graphene and graphite as filler material in a polymer matrix, deliver unprecedented thermal conductivity (3-10 W/mK).Heat sinks
A heat sink is a highly thermal conductive device that is designed with a maximized surface area to provide effective heat dissipation. The heat sink is the last and most influential part of the system thermal path. It seeks to pull heat away from the LED module through an MCPCB (and a TIM most often) so as to maintain the junction temperature of the LEDs within safe operating limits. Heat is drawn out of the LED junction by conduction into the heat sink. Convection is the main mode of heat transfer to extract heat from the heat sink to the surrounding air. Hence, to provide high volume thermal conduction an LED heat sink is typically made from aluminum (90-240 W/mK), copper (400 W/mK), ceramics (100-200 W/mK), and materials that possess high thermal conductivity. The geometry of the heat sink is designed with an aim to maximize the effective surface area around which air is circulating while facilitating the ambient air flow through an effective aerodynamic design.Aluminum offers significant advantages as a heat sinking material because of its high dimensional stability, excellent thermal conductivity, good corrosion resistance, superior finishing characteristics, and full recyclability. High purity aluminum has a thermal conductivity at room temperature of up to 210 W/mK. Aluminum is often formulated with various elements, including silicon, iron, manganese, magnesium, nickel, zinc, titanium, or others, to enhance particular properties or support specific manufacturing processes.
Selection of thermally conductive materials is very important but, even using the same material different manufacturing processes can render different thermal characteristics for a heat sink. Material selection must consider manufacturing processes which determine the molecular density for conducting heat and the structural integrity of the heat sink. There're many ways to manufacture a heat sink. The most commonly used manufacturing processes are die casting, forging, and extrusion. Other processes include machining, stamping, bonding, folding, and skiving.
Die casting is accomplished by injecting molten metal under high pressure into reusable metal dies or molds. In the lighting industry, die cast heat sinks are ubiquitously found in high bay lights, street lights, explosion proof lights, flood lights, downlights, and other LED luminaires that require a cost-effective, thermally efficient and geometrically adaptable heat sinking solution. Die casting is based on aluminum alloys, e.g. zinc (Zi) based or silicon (Si) based alloys. Thermal conductivity varies in different compositions of aluminum alloys. ADC12, a silicon based alloy, has a thermal conductivity of 96 W/mk. Zi based alloys (e.g. Zamak 3) have a thermal conductivity in the range of 105-113 W/mK.
Forged heat sinks are manufactured by punching raw material into a molding die. While hot forging is inherently easier, cold forging, which produces no air bubbles and does not trap impurities in the material, is preferred in heat sink production. Cold forged components have a higher thermal conductivity and structural stability than die casting parts, although intricate geometries simply not possible using cold forging. Cold forged heat sink using aluminum alloys in the 1000 range have thermal conductivities ranging from 220 W/mk to 240 W/mk. Cold forged 606x range (e.g. AL6063) aluminum alloys have a typical thermal conductivity of 200 W/mk. The thermal conductivity of the cold forged 7xxx range varies between 115-222 W/mk.
Extruded heat sinks are made by pushing or drawing a material through a die which is shaped to impart a specific form to the extrusion. This process creates a product with greater density for aluminum extrusions and renders a significant higher thermal conductivity than die cast aluminum heat sinks. Aluminum extrusions offer thermal conductivities in the 200-215 W/mK range. Although very complex cross-sections can be created, extrusion is only a 2D process incapable of creating heat sinks with a high fin density and 3D geometry. Aluminum extrusions can use only 6xxx alloys (e.g. 6063) and are suitable only for cooling linear LED modules.
A heat sink with a greater surface area is often achieved by adding an array of fins. Different fin shapes and densities can be designed to provide convective dissipation capacity and direct the airflow as required, while also allowing a heat sink to be confined to a given footprint.
Although a heat sink will also dissipate heat by thermal radiation, it radiates little heat in LED applications because electromagnetic propagation requires a fairly high surface temperature. Heat sinks are often powder coated or anodized to improve corrosion resistance and reduce thermal resistance. A concurrent benefit of surface treatment is that it also provides a greater radiative emissivity.
Active Cooling
In most thermal management solutions, heat is dissipated using the free flow of air that circulates in the natural environment without an introduction of additional energy to enhance thermal transfer. With the proper heat sink design, passive thermal management through natural convection can be a very effective. However, passive heat sinks alone cannot handle thermal management efficiently when they are employed in higher power density lighting systems or applications where air flow is insufficient and correspondingly so is the heat transfer coefficient. As such, active thermal management should be considered. Active cooling systems rely on an external mechanism to force a fluid (air or liquid) into motion and increase the heat transfer coefficient.Actives cooling solutions can be implemented using fan sinks, heat pipes, liquid cooling, Peltier devices, or synthetic jet cooling. In fan-driven forced convection systems, an electrically powered fan blows a sufficient quantity of air along the surface of the heat sink. The fan typically leverages magnetic levitation technology to eliminate noise that would otherwise occur in fans utilizing a bearing. A heat pipe, which may be used alone or in combination with a heat sink, makes use of thermal conductivity and phase transition between evaporation and condensation to transfer heat between two interfaces. LED lighting systems rarely rely on the costly liquid cooling systems which dissipate heat by means of the convection or circulation of a liquid. Peltier cooling devices are seldom a choice for LED cooling because they consume an excessive amount of power. A synthetic jet utilizes an electromagnetic actuator which can produces a rapid-fire pulses of turbulent air. This technology has cooling possibilities comparable to a fan, yet offer better reliability and produce less noise.