Table of Contents Hide
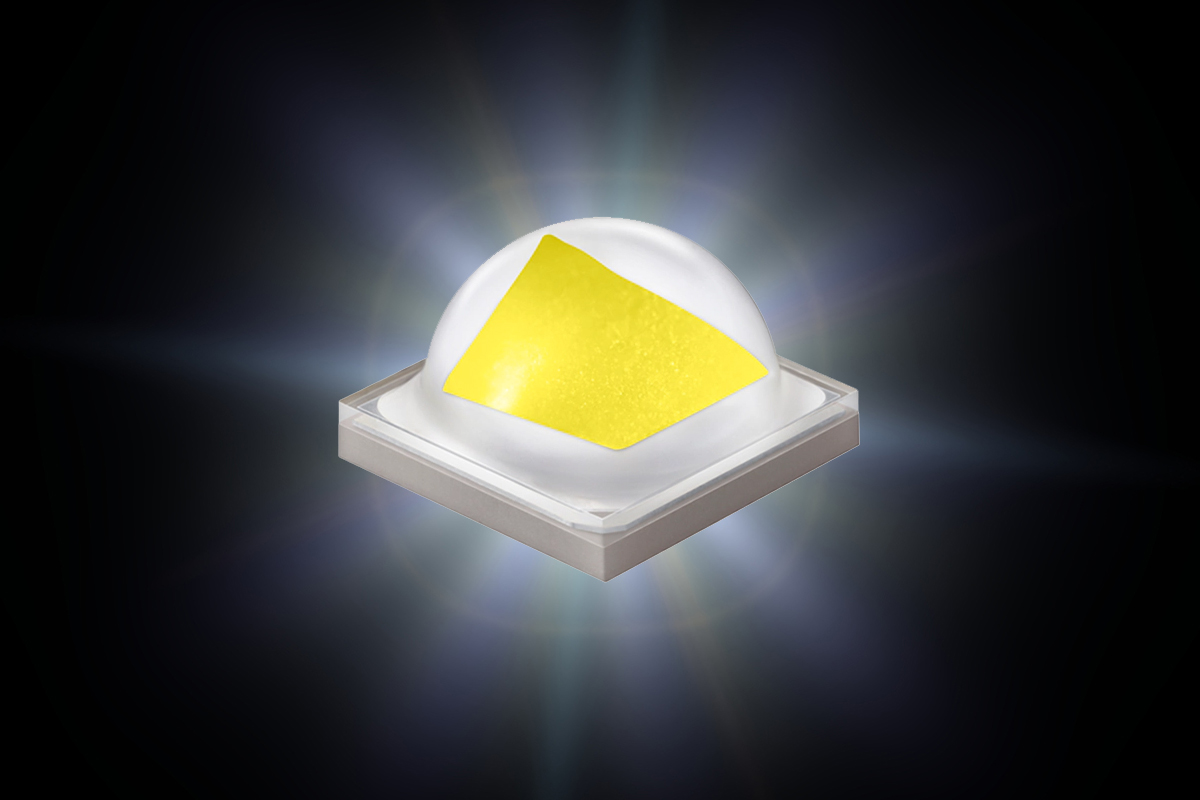
What Is a High Power LED
A high power LED is commonly defined as an LED package that operates at 1 watt of power or higher. This high flux density light source may be driven at current from hundreds of mA to more than an ampere, and a single LED can pump out hundreds or even thousands of lumens. High power LEDs are designed to deliver dependable lighting for high lumen applications in industrial facilities, sports venues and outdoor environments. These applications include high bay lighting, flood lighting, street lighting, and high mast lighting. High power LEDs are also used in vehicle-mounted spotlights, portable torches and flashlights. There is a high upfront cost of investing in luminaires that use high power LEDs as the light source. Nevertheless, the optical power, lumen maintenance and reliability of high power LEDs often translate to a return on investment that is significantly higher than that from using mid-power LEDs. In fact, the higher operating temperatures and compact footprint of high power ceramic packages enable shrinked heat sink design and offer tremendous savings in PCB, TIR reflectors and diffuser optics, which account for a big portion of the BOM cost for systems using mid-power LEDs.Architecture
A phosphor-converted (PC) high power LED package consists of a large chip (die) or a multi-die array mounted onto a ceramic substrate via a metal interconnect layer. A phosphor conformal coating is applied over the LED chip and then a clear hemispherical silicone lens is over-molded onto the package. In a typical single-wire-bond-connection package, the electrical interconnect layer connects the LED chip to the anode on the underside of the ceramic substrate. The cathode of the junction may be located on the top of the die, which is connected to the adjacent negative terminal using a bond wire. The underside of the ceramic substrate typically includes three metal pads: the negative and positive terminal pads to be reflow soldered to printed circuit pads, and a thermal mad to maximize thermal contact area with the metal core PCB. A silicone dome lens which has a lower refractive index is often mounted on the LED to increase the collection cone and allow the LED to extract as much of the light as possible. In contrast to cylindrical- and elliptical-shaped lenses, the hemispherical shape of the dome lens facilitates more uniform thermal dissipation along the thermal path from the LED chip to the lens. To protect the LED chip from electrostatic discharge (ESD), a transient voltage suppressor (TVS) chip is mounted on the metallized ceramic substrate. Compared with the PLCC (plastic leaded chip carrier) architecture for mid-power packages, the ceramic architecture provides a more robust construction that dramatically increases package reliability and the projected lumen maintenance.Die Fabrication
White LEDs utilize a direct bandgap semiconductor known as indium gallium nitride (InGaN) to produce an emission with a dominant wavelength in the blue portion of the visible light spectrum. The epitaxial layers which form the p-n junction are grown on a carrier substrate made of single crystal materials such as silicon, sapphire, silicon carbide, or gallium arsenide. The GaN-based devices are dominantly fabricated on a sapphire substrate. Sapphire is a crystalline aluminum oxide which is chemically and thermally stable, and is resistant to erosion by oxygen or alkali. Its high-melting point makes it possible to perform a high-temperature manufacturing process. Sapphire supports a relatively high quality GaN epitaxial growth with no substantial lattice mismatch between its crystal lattice structure and that of InGaN. These qualities, combined with excellent processability and economies of scale, make sapphire hard to be challenged by other substrate materials.Sapphire is not without disadvantages, however, such as the not-so-perfect lattice match to InGaN and low thermal conductivity. The large mismatch introduces microcracks (threading dislocations) into the diode structure. A high dislocation density in the epitaxial films compromises optoelectronic efficiency because recombinations of electrons and holes that occur at sites of microcracks are primarily nonradiative. Sapphire's low thermal conductivity undermines heat dissipation from the p-n junction of the face-up mounted LED chips.
Compared with sapphire substrates, silicon carbide (SiC) substrates more closely match the lattice InGaN structure and thus enable more radiative recombinations in the active region. Another major benefit of fabricating epitaxial layers on SiC substrates is that SiC has approximately the same thermal conductivity as copper. This thermal quality makes SiC-based LEDs inherently advantageous in high power lighting applications. However, to date only Cree has championed the use of SiC substrates for LED fabrication. This is because the production of SiC substrates involves a complex and costly process to reduce crystal defect densities.
The ultimate solution will be the GaN-on-GaN technology which fundamentally removes epitaxial constraints of growing GaN or InGaN on foreign substrates. In GaN-on-GaN LED dies, both lattice and CTE are perfectly matched and this means an extremely low dislocation density in the epitaxial film. What's more, GaN-on-GaN LEDs can operate at ten times the current density of traditional LEDs without efficiency droop due to current crowding. As a result, GaN-on-GaN high power LEDs provide a quantum leap in light output compared with GaN-on- Sapphire and GaN-on- SiC counterparts with the same LES (light emitting surface).
LED Packaging
Packaging plays multiple roles in that it protects the semiconductor die from being damaged physically or chemically, interfaces the die to its operating interface mechanically and electrically, provides wavelength conversion and color mixing to produce white light, and extracts heat from the active region of the LED. LED package platforms, depending on their architecture, materials of construction and packaging processes, have different intrinsic characteristics. The most challenging issue when operating a high power LED is to dissipate the considerable amount of heat produced around the LED junction. While mid-power LEDs with a PLCC architecture make the cost reduction trend possible, the efficacy and cost benefits of these LEDs are literally achieved at the expense of compromised lumen maintenance and color stability. As the LED draws more power, more heat is generated. Mid-power packages built on plastic substrates often fail to stand up to the challenge of high thermal stress, and this is what makes high power LEDs sensible.The fundamental packaging philosophy of high power LED packages revolves around maximizing material thermal conductivity and effective surface area of the thermal path while minimizing the length of the thermal path and the coefficient of thermal expansion (CTE) mismatch between components. The lead frames of mid-power packages are molded into polyphthalamide (PPA), polycyclohexylenedimethylene terephthalate (PCT), or epoxy molding compound (EMC) housings. These plastic housing are not only poor in thermal conduction, but also prone to degradation under high thermal stress and may result in irreversible chemical bond breakages or rearrangements of the bonds around carbon atoms. Ceramics are thermally stable and conductive, and also optically and chemically inert. From the thermal performance and optical stability perspectives ceramic substrates are fundamentally superior to plastic substrates. Currently two types of ceramics make up the vast majority of high power LED substrates: alumina and aluminium nitride. Alumina, or aluminium oxide (Al₂O₃) is a relatively affordable option and offers (depending on purity) in the range of 20-30 W/mK. Aluminium nitride has excellent thermal conductivity (140-180 W/mK) but is expensive since this material is synthesized in an exceptionally high-temperature process.
What differentiates high power LED packages from the mid-power counterparts is not simply the use of ceramics as the package substrate. The robust thermal performance of high power LEDs is also attributable to their effective thermal design. In high power LEDs, the ceramic package substrates are metallized with copper layers to form an anode pad, a cathode pad and an electrically insulated thermal pad on the underside of the substrate. On the topside of the ceramic substrate the LED die is mounted on the metallized surface which dissipates the junction heat and serves as the anode electrode. The epitaxial n-type layer is wire-bonded to the topside cathode copper layer using a gold, palladium-coated copper, or silver wire. The topside anode and cathode have through-hole connections to the backside anode and cathode pads. Thermal vias are widely used with ceramic substrates to reduce the thermal resistance. A thermal via is a thermally conductive conduit that can be open, plugged, filled or filled and capped.
High power LED packages have a thin phosphor layer formulated on die using a conformal coating technique. Conformal coating of phosphor within polymeric matrix on the LED die produces very consistent coating thicknesses around the entire die. This ensures homogeneous and consistent color across the beam. Unlike cavity encapsulation designed for PLCC packages, phosphor conformal coating for high power LEDs uses minimal binder. The high power LED architecture often creates high thermal stresses to the phosphor and binder materials. Therefore the thermal stability of the phosphor conformal coating is of vital importance. Phosphors are typically combined with the polymers such as silicones and epoxies. At present, all of the high power LED packages use silicones as the binder material. Silicones do not decompose until 350–380 °C and have high thermal diffusivity to efficiently dissipate the heat generated in the phosphor. This material also exhibits high optical transparency and high aging stability to photo-oxidation. Its mechanical softness allows for preservation of wire bond. However, silicone high moisture and gas permeability. Thus, care must be taken to prevent diffusion of volatile organic compound (VOC) gas molecules into the silicone overcoat.
LED Efficiency
The efficiency of a high power LED can be decomposed into the external quantum efficiency (EQE) and the packaging efficiency.EQE is associated with losses of electrons and of photons which occur when carrier electrons recombine with holes within the semiconductor junction to release energy in the form of photons. External quantum efficiency can be broken down as the product of the internal quantum efficiency (IQE) and the photon extraction efficiency (EXE). IQE, also known as radiative efficiency, is determined by both carrier injection efficiency (CIE) and carrier radiative recombination efficiency (RRE). CIE relates to the proportion of positive and negative charge carriers injected into the active region. RRE is the ratio of radiative electron-hole pairs to the total number of pairs that recombine in the active region. Photon extraction efficiency refers to the ratio of the photons extracted from the semiconductor die vs generated at the semiconductor junction. Photons can be internally reflected and trapped in the high refractive index of the epi-material, thus resulting in optical loss.
The internal quantum efficiency losses can be as a consequence of a high dislocation density in the epitaxial films. Threading dislocations are microcracks induced by the large mismatch between its crystal lattice structure and that of GaN. This type of irregular arrangements of atoms in crystals leads to recombination of the electron-hole pair in a non-radiative manner. Threading dislocations caused by the lattice mismatch form in highest densities on sapphire based GaN LEDs. Silicon carbide shows promise as a substrate for its close lattice match to GaN. Along with a higher thermal conductivity of a SiC substrate, the recombination efficiency of GaN-on-SiC devices will always outperform GaN-on-Sapphire and GaN-on-Silicon devices. However, the highest efficiency LEDs will be those made from GaN-on-GaN dies which have a perfect lattice match.
The atomic defect generation and growth can be accelerated at high drive currents and high operating temperatures. As the injection current density is increased beyond the saturation level, Auger recombination dominates. This microcosmic process causes a non-radiative carrier recombination which release heat instead of light. Such a phenomenon is known as efficiency droop or current density droop. The rate of non-radiative Auger recombination is not only accelerated when the carrier concentration is high, it is also exponentially dependent on the junction temperature. As high current density is always accompanied by high heat flux density, the non-radiative recombination increases with higher junction temperatures. This is because the increased differences in the thermal coefficient of expansion between the deposited semiconductor and substrate result in more threading dislocations. The reduction of the optical power when the junction temperature is increased is called thermal droop.
Different package architectures yield a large efficacy gap between the high power LEDs and mid-power LEDs. Thanks to a highly reflective cavity that significantly improves light extraction, today's mid-power LEDs can offer a high luminous efficacy of over 200 lm/W (4000K 80 CRI). The packaging efficiency loss in the high power LEDs is substantially higher since the LED chip is mounted on a non-reflective copper layer. The highest luminous efficacy for Gan-on-Sapphire high power LEDs currently available on the market is typically at 160 lm/W (4000K 80 CRI). In ceramic LED architectures, light extraction at the package level is enhanced by reducing the refractive indexes of the phosphor coating and through the use of secondary light outcoupling optics, e.g. clear dome lenses. As with all PC-LEDs, a significant portion of short wavelength light is not extracted from the package due to mixing/scattering/absorption losses. In addition to improving phosphor quantum efficiency and optical efficiency of the phosphor coating, a potential opportunity for efficiency improvement is to develop down-converters with a narrow FWHM (full width half maximum) red phosphor band.
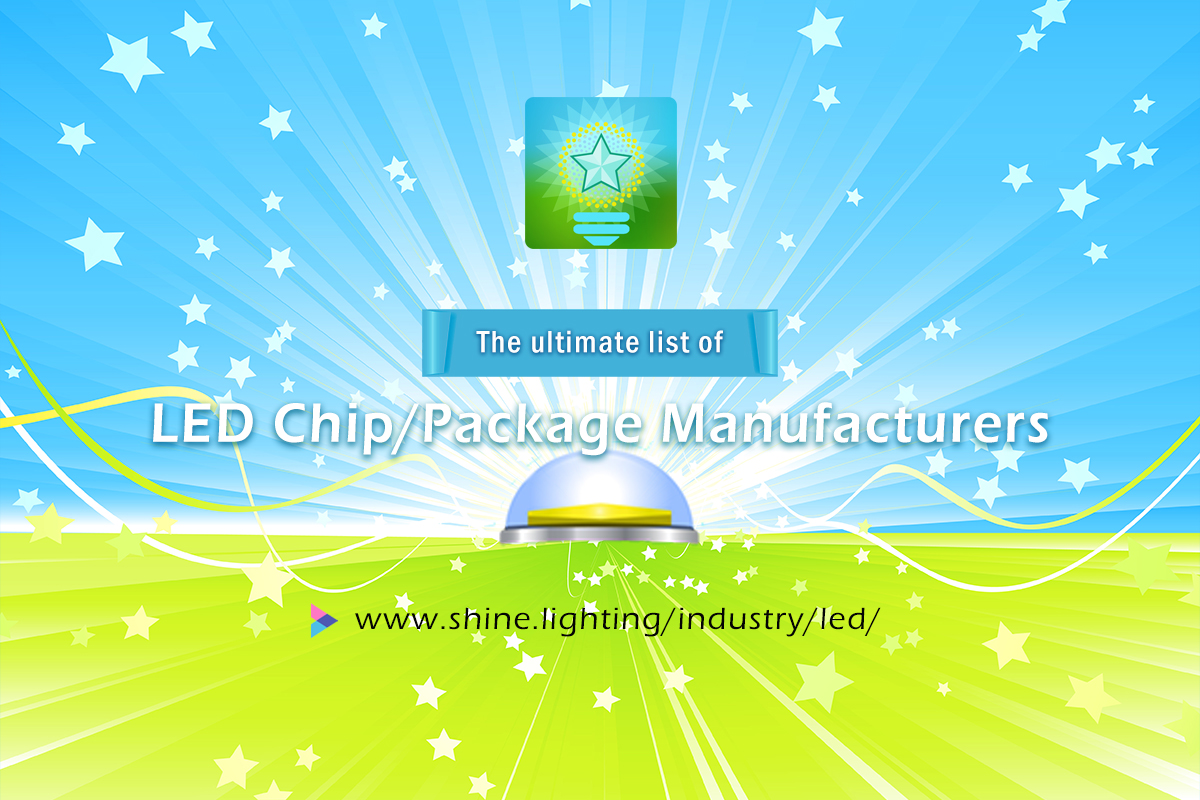
Lumen Maintenance
While mid-power LED packages may have a better lumens per watt ratio, high power LED packages win out in lumen maintenance. The useful life (defined as 70% lumen maintenance) of an LED are primarily temperature dependent. The plastic housings and lead frames of mid-power packages have a strong inclination towards thermal degradation and photo-oxidation. The thermal conduction capacity of PLCC packages is always the bottleneck and therefore thermal buildup is very likely to occur. Heat flux concentration at the semiconductor junction can cause irreversible lumen depreciation in mid-power LED packages at a rate much higher than that in high power LEDs. High power packages come with a massively improved thermal design. A thermally conductive ceramic substrate metallized with a copper layer provides a considerably large thermal interface. An array of thermal vias facilitates heat transfer. High chemical and temperature stability makes the ceramic substrate exempt from photo-oxidation reaction, which is one of the dominant degradation mechanism in mid-power packages. High power LEDs in general lose less than 10% of their light output at 30,000 hours, and it's not surprising for mid-power LED to lose 30% light at the same time point.For high power LEDs, the major cause of lumen maintenance failure is degradation and quenching of the phosphor coating. Operating at high optical flux densities and the Stokes shift from shorter wavelengths to longer wavelengths produce the most thermal stress to the phosphor and binder materials. Therefore, serious consideration must be given to thermal stability of the encapsulating polymeric material. The quantum efficiency of the phosphor material is required to be as high as possible so that minimal optical power is converted into waste heat. Lumen depreciation can also be implications of chromaticity shifts associated with various degradation mechanisms of packaging materials.
Color Stability
Although lumen maintenance is important, shift in color coordinates or color temperature can be more problematic. The dominant mechanisms that cause high power LEDs to produce chromaticity shifts include thermal degradation of the phosphor coating, diffusion of VOCs in the silicone-based binder, photo-oxidation induced discoloration of the secondary lens, moisture-polymer reactions, and delamination/cracking at the chip/phosphor interface.- Loss in phosphor quantum efficiency due to thermal quenching or chemical change a spectral shift will produce a blue shift.
- The phosphor blend using a YAG:Ce yellow phosphor and a nitride red phosphor in warm white high power LEDs tends to develop a color shift toward the green direction under oxidizing environments.
- Thermal decomposition of phosphor coating develops yellow color due to accumulation of chromophores.
- The delamination at the chip/phosphor interface will cause a chromaticity shift towards the yellow direction.
- The photo-oxidation and thermal degradation of polymeric materials impair the optical transparency of the secondary dome lenses and lead to discoloration and yellowing.
- VOCs inside the silicone-based binder may partially oxidize during the presence of heat or light and create a silicone discoloration.
Color Reproduction
The color reproduction performance of high power LEDs, which is measured using the color rendering index (CRI), was conventionally not considered as critical as other specifications like luminous efficacy, lumen depreciation and color stability. This is because these light sources are typically used in outdoor and industrial environments where the color quality of a light source is not a priority consideration. The fundamental cause of "overlooking" the color rendition of high power LED s is that there's a trade-off between luminous efficiency and spectral quality. To achieve a high CRI, a significant portion of blue wavelengths needs to be down-converted into longer wavelengths which allows the human eye to perceive a full spectrum of colors with high fidelity. Wide Stokes shift results in a significant energy loss and thus the luminous efficacy of the light source is drastically reduced. On the reverse side, less phosphor down-conversion means less waste in optical power, but the color rendition would be poor since there's an inadequate amount of longer wavelengths in the light spectrum. In general, every 10-point increase in CRI will cause a 15% decrease in luminous efficacy.Similar to the trend of mid-power LEDs inching into the outdoor and industrial markets for their competitive lm/$, the excellent lumen maintenance and high color stability of high power LEDs appeal to an increasing number of indoor applications. To accommodate indoor and other color-critical applications, high power LEDs with a minimum CRI of 90 are available. The high CRI version that achieves desired spectral characteristics using wide band red phosphors inevitably comes with a lower luminous efficacy compared with the 70/80 CRI LEDs. A recent trend is to use quantum dots as a narrow band red phosphor to enhance color quality without compromising the efficiency of the LED.
LED Binning
Binning is a process of sorting LEDs based on chromaticity, lumen output, and forward voltage. In the production of LEDs, the die fabrication and packaging processes create inherent variations that impact the output of LEDs. The magnitude of differences in both output intensity and peak wavelength between LEDs therefore must be controlled to meet a consistency protocol. Binning for light output and forward voltage is a very straightforward practice. Chromaticity binning is more complex process as the variation in chromaticity extends to a zone. Lighting manufacturers use either the Standard Deviation Color Matching (SDCM) MacAdam ellipses or the American National Standards Institute (ANSI) parallelograms to define the color tolerances.The SDCM method defines elliptical zones in the CIE 1931 (x,y) chromaticity diagram, whereby 1SDCM equals 1-step MacAdam ellipse. The smaller the ellipse, the less color variation. Color bins are defined by ANSI as parallelograms which overlay the MacAdam ellipses on the CIE color map. Chromaticity deviations of two to three levels (2/3-step MacAdam ellipse) are considered barely perceptible. For most applications color control with a 5-step MacAdam ellipse is still sufficient. Even color bins that hit a 7SDCM or 8SDCM color point can be tolerable in less color-tight outdoor lighting applications because the human eye cannot differentiate between hues that are spaced from each other by up to seven steps of ellipse.